For optimal results, industrial parts cleaning requires a well-structured process. This article delves into the essential stages of industrial parts cleaning, shedding light on multistage processes, their significance, as well as the methods used to ensure parts meet stringent cleanliness and dryness standards.
From the initial wash to the final cool-down, each stage plays a vital role in preparing components for subsequent manufacturing or packaging, ultimately contributing to operational success.
The Need for Multistage Parts Washing
Cleaning industrial parts isn’t a one-size-fits-all endeavor. The type and number of stages necessary for a washing application depend largely on the type of residue left on the parts, the part’s shape, dimensions, and material, and the soil level. Residue can take the form of either solid or liquid matter. Solid residue often includes excess fines and chips, while liquid residue may consist of oils, coolants, and lubricants.
To effectively remove these residues, industrial parts cleaning typically involves a variety of cleaning stages.
Overview of Cleaning Stages
- Wash Stage: In this initial and crucial stage, high-pressure sprays or submersion in cleaning solutions clean the parts. This process removes most of the soil and contaminants. The stage often employs the highest water pressure and volume to effectively dislodge residues from the parts.
- Rinse Stage: After washing, this step involves rinsing the parts with water to eliminate any remaining cleaning agents or loosened contaminants. At this point, you may also apply a rust preventative (RP) to the parts. The rinse stage usually features a lower-pressure spray and may repeat to ensure thorough cleaning.
- Moisture Blow-Off Stage: This stage aims to remove residual moisture from the parts following the washing and rinsing. High-velocity air blowers and strategically placed nozzles effectively dislodge water droplets, preparing the parts for the drying stage without completely drying them.
- Drying Stage: In this stage, a controlled environment dries the parts. Methods include using gas, electric, or steam-heated cabinets, vacuum systems, or high-velocity air blowers. This stage ensures the complete drying of the parts, free from moisture, to meet the customer’s required dryness standards.
- Cool-Down Stage: This final phase involves cooling the parts down to a safe handling temperature, typically using ambient air blowers. This step is crucial, especially when immediate packaging or handling is necessary post-cleaning. It helps to prevent any handling or packaging issues due to heat.
Multistage Processes: Customization for Optimal Cleaning
In multistage parts washing processes, customization is essential to achieve optimal cleaning results. The style of industrial parts washer you select plays a role in the stages that are available for your application. For this reason, you should determine the best-suited style of washer for your project.
For example: Certain parts washers, like Conveyor Parts Washers, can be designed for either single or multiple stages (including wash, rinse, blow-off, drying, and cool-down), while others, such as Cabinet Washers, are limited to using wash, rinse, and blow-off stages.
Washer Type | Washer Model | # of Stages/Sections Available |
Conveyor Washers | Inline U-Bend Monorail | Usually 2-5 stages: Wash, Rinse, Blow-Off, Drying, and Cool-Down |
Immersion Washers | Standard Agitation Ultrasonic | Typically 1 stage: Wash *Could consist of multiple separate stages to achieve wash, rinse, and dry. |
Rotary Drum Washers | Standard | Up to 5 stages: Wash, Rinse, Blow-Off, Drying, and Cool-Down |
Cabinet Washers | Front-Load Top-Load | 1-3 stages: Wash, Rinse, Blow-Off |
After determining the right parts washer for you, tailor the sequence and duration of cleaning stages to your specific project. The configuration of stages can vary depending on the residue and soil level of the parts.
Some projects may require only a few stages, while others may require multiple stages to achieve your desired cleanliness and dryness results.
Here are a few examples of multistage processes. Keep in mind – your application can range from a few to multiple stages to achieve your desired results.
- 2 Stage: Wash & Blow-Off
- 3 Stage: Wash, Rinse/Rust Inhibit, and Blow-Off
- 5 Stage: Wash, Rinse, 2nd Rinse, Blow-Off, Drying Units
- 5-Stage: Wash, Rinse, Rinse, Dry, Cool-Down
- 7-Stage: Wash, Rinse, DI Rinse (recirculation), DI Rinse (fresh), Blow-Off, Dry, Cool-Down
Wash Stage: The First Step in Parts Cleaning
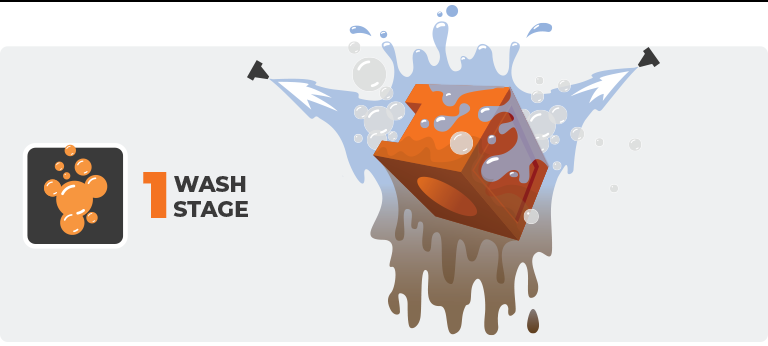
All styles of industrial parts cleaning equipment include a wash stage. This stage removes the bulk of the soil and contaminants from the parts.
This stage typically uses the highest spray pressure, and the most water compared to other cleaning stages. By adjusting these factors to match the part’s needs and residue type, the wash stage sets the stage for successful cleaning. Depending on the style of washer you select, the method of washing varies.
Conveyor Washers: Wash Stage
In Conveyor Washers, the wash stage typically relies on adjustable spray nozzles that are positioned throughout the conveyor’s tunnel. The high-pressure nozzles spray a mixture of water and compounds across the parts’ surfaces as they move down the conveyor. This allows access to the top, bottom, and sides of the parts.
The operator controls the conveyor belt speed to increase or decrease the wash time. The wash time depends on the soil level of the parts, effectively dislodging, and removing residue and contaminants. You can also add indexing features to pause the conveyor and part at specific spray or process stations.
Immersion Washers: Wash Stage
In Immersion Washers, the parts are typically placed directly on a platform or in a basket. They are then submerged in an agitated cleaning solution. The model of the Immersion Washer will determine the next step in the washing process.
- Standard agitation model: the parts agitate up in down in the cleaning solution.
- Ultrasonic model: the immersion washer transmits high-energy and high-frequency sound waves throughout the cleaning bath. This provides an intense cleaning and scrubbing action to the parts.
Rotary Drum Washers: Wash Stage
Rotary Drum Washers utilize both spray nozzles and submersion to effectively clean parts. Parts are fed into the corkscrew-shaped rotary drum. While the parts are spiraled through the cleaning drum chamber, they are partially submerged in a cleaning solution and sprayed via a nozzle-equipped manifold. The length and spacing of the drum can be fully customized based on the customer’s application.
Cabinet Washers: Wash Stage
Cabinet Washers also utilize high-pressure adjustable spray nozzles. Unlike Conveyor Washers, the spray nozzles are positioned around an enclosed platform. Once the parts are loaded into the machine and the door is shut, the turntable rotates (if equipped). This helps expose all the part sides to high-pressure spray nozzles.
Rinse Stage: Ensuring Residue-Free Results
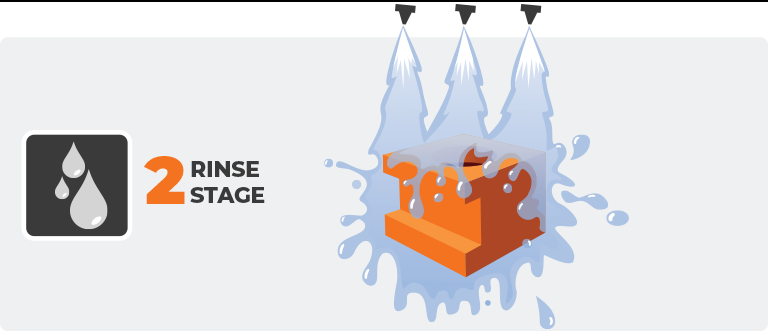
The rinse stage, which usually follows the wash stage, aims to thoroughly rinse and remove any soap or residues from the parts. Additional rinses may follow to minimize water spotting and/or apply additional chemical treatment. This stage utilizes spray nozzles and uses a lower-pressure spray in comparison to the wash stage. Due to using lower pressure, the rinse stage uses lower water volume.
Rinsing Configurations
You can use multiple types of rinse configurations during the rinse stage. Below are some of the most common rinse configurations:
Recirculatory Rinse
This rinse reuses the water and/or solutions to rinse residue from the prior stage. This residue is typically soap. Often, this rinse stage involves heating and pumping the solution through a spray system similar to the one used in the wash stage.
Rinse-to-Drain
Unlike recirculating, this is a single-use rinse. The building or facility directly supplies the water, which is sometimes treated. Once sprayed, the water will go directly to the drain. This type of rinse will often use fewer nozzles and lower pressure than a recirculating rinse.
Rust and Corrosion Inhibitors
Depending on the part’s material and the chemicals and compounds used during the washing stage, you may need to use rust or corrosion inhibitors. This involves adding a rust or corrosion-inhibiting chemical into the water tank during the rinse stage.
Rust and corrosion inhibitors are essential for ferrous parts made of materials prone to rusting, such as metal. Integrating these inhibitors into the rinse stage is crucial for preventing future corrosion and rust formation. It also helps enhance the longevity of the cleaned components.
Treated Water Rinse
You often use softened water, deionized water, or RO water (reverse osmosis) to minimize water spotting on parts, typically after a recirculatory rinse stage.
Moisture Blow-Off Stage: Preparing for Drying
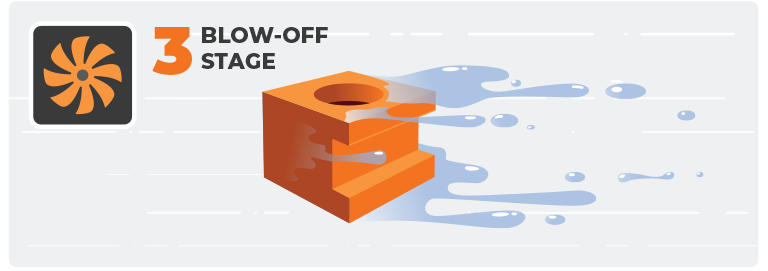
This stage is not intended to completely dry the parts. The primary objective of the moisture blow-off stage is to remove residual moisture or water droplets that may cling to the parts after the wash and rinse stages. This stage also helps prepare parts for subsequent processes or assembly.
As part of this process, high-velocity air blowers or compressed air nozzles are utilized to dislodge moisture from the parts. These nozzles can be adjusted to target specific parts or areas that require thorough drying. The method used during the moisture blow-off stage depends on the geometry of the part and the requirements for the next step in the manufacturing process. The duration of the moisture blow-off stage can vary depending on the part size and the extent of moisture present.
For example: Parts with depressions or blind holes that hold water could take more time to remove the standing water. Whereas parts that don’t hold water are relatively easy to blow off and remove moisture.
Drying Stage: Achieving the Final Dryness
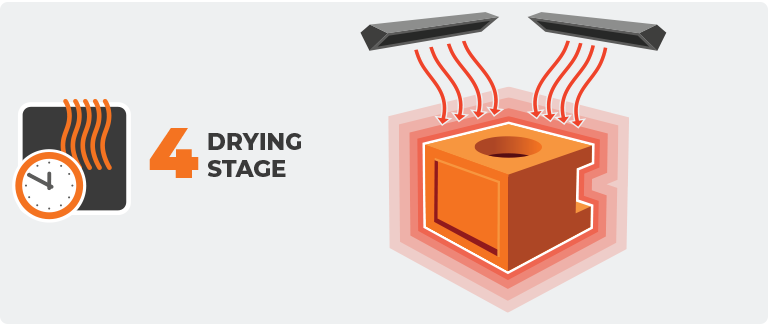
The drying stage, a crucial step following cleaning and rinsing, achieves final dryness. This process, customized for different parts and industry standards, often involves various drying methods.
Gas or electric-heated cabinets are common, creating a controlled environment for drying by elevating temperatures and speeding up moisture evaporation. Additionally, high-velocity air blowers play a key role in directing and circulating warm, dry air, ensuring thorough drying across all parts’ surfaces.
In addition to heated cabinets, you can also use vacuum drying systems. Vacuum drying systems reduce the pressure to lower the water’s boiling point and prevent heat-related damage to sensitive components.
The drying stage may also incorporate additional mechanisms for removing remaining humidity from prior cleaning stages. Some of these mechanisms include desiccant dryers or dehumidifiers. Through this comprehensive drying approach, parts emerge completely dry and free of moisture or contaminants. This helps them meet stringent industry standards for cleanliness and dryness. As a result, they become well-prepared for subsequent manufacturing or packaging. This minimizes the risk of issues like corrosion or contamination in downstream processes.
Cool-Down Stage: Preparing for Packaging
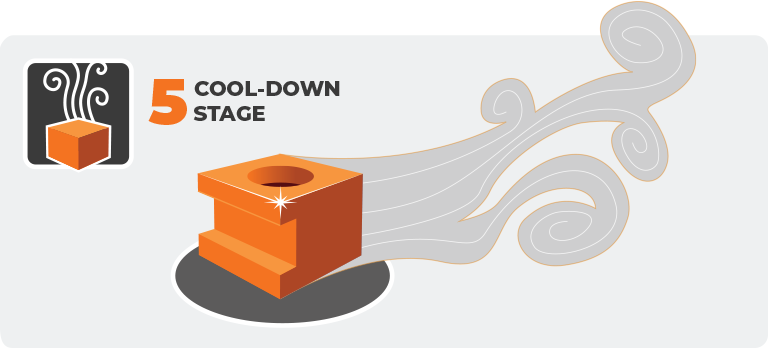
This stage usually serves as the final phase in the washing process. It involves using extended dryers or conveyor belts with mounted fans to blow ambient air over the parts till they reach their desired temperature. This step enables operators to safely handle and package the parts, often eliminating the necessity for gloves. The cool-down stage holds particular significance when immediate packaging follows the washing process.
For example: Packaging parts while they are still warm without this cooling phase can result in condensation forming on the components, potentially causing problems like rusting.
Conclusion
Understanding the various stages of industrial parts cleaning is essential for achieving efficient and effective results. Each stage plays a critical role in ensuring the cleanliness and quality of parts, ultimately contributing to operational success. As you explore the world of industrial finishing and washing, consider the importance of these stages in your manufacturing process.
At ALMCO, we specialize in providing top-notch solutions in industrial finishing and washing. Our expertise in multistage parts washing systems ensures that your parts meet the highest cleanliness standards. Contact us today for further information or to discuss how our solutions can benefit your industrial manufacturing processes.
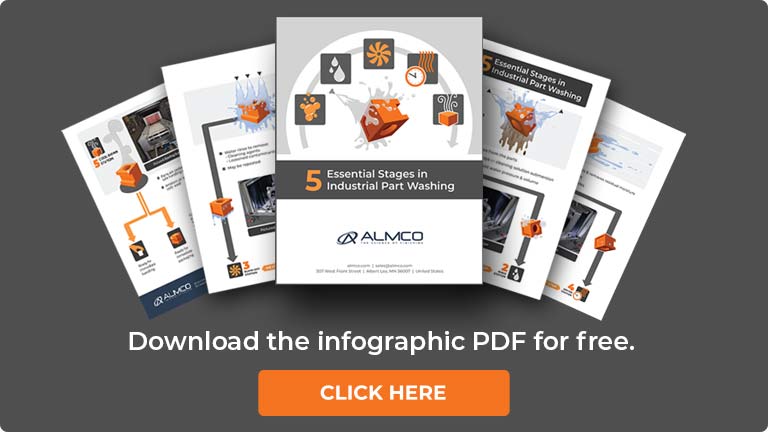