Industrial parts washing and drying systems encompass a wide spectrum of automation levels.
This article delves into the various levels of automation available, helping users understand the spectrum from manual to fully automated systems.
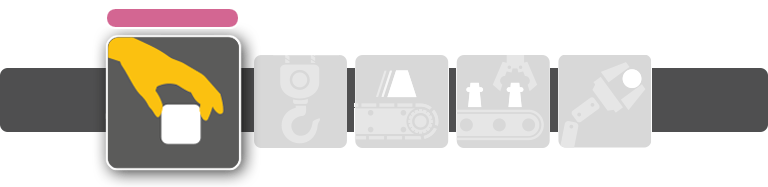
Complete Manual Systems
Complete manual systems represent the most basic form of parts washing, where every aspect of the process is done by hand. This includes loading, operating, and unloading the machine. These systems are straightforward and require no complex machinery but demand significant human labor.
This method is applicable to all styles of industrial parts washing systems such as Cabinet Washers, Inline Washers, Drum Washers, and Immersion Washers.
In this process, parts can be loaded individually or in baskets.
Manual Considerations
- Labor-Intensive: Ideal for small-scale operations or where automation is not feasible.
- Flexibility: Easily adaptable to different types of parts without additional investment.
- Ergonomic Risks: Prolonged manual handling can pose physical strain on workers.
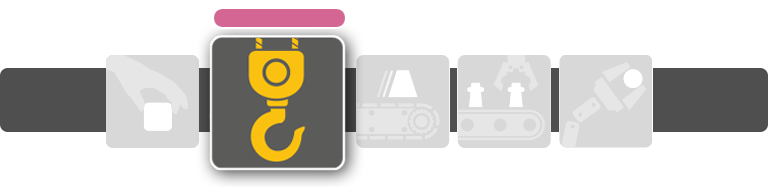
Hoist-Loaded Systems
Hoist-loaded systems combine manual effort and mechanical assistance. Operators still play a role in the loading and unloading of parts but are assisted by a hoist or crane to lift heavy parts into the washing system.
This semi-automated approach bridges the gap between manual labor and full automation.
Operators use hoists or cranes to load and unload parts, reducing the physical strain of handling heavy components.
Hoist-Loaded Considerations
- Cost-Effective Upgrade: Enhances efficiency without the full cost of automation.
- Safety Improvement: Reduces the risk of injuries associated with heavy lifting.
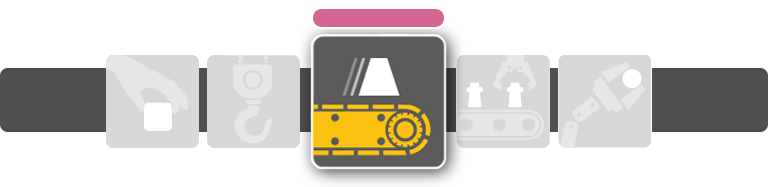
Conveyorized Systems
Systems that utilize conveyors represent a significant step in automation for industrial parts washing. Conveyorized systems employ various types of conveyors to automate and streamline the movement of parts through the washing process. These systems usually eliminate the need for manual interaction during the loading/unloading process, reducing manual labor and increasing efficiency.
Conveyorized Considerations
- Types of Conveyors: Various designs cater to different parts and processes.
- Continuous Operation: Ideal for medium to high-volume production lines.
- Integration Potential: This system can be integrated with other automated systems for further efficiency.
Types of Conveyors
There are a variety of conveyor options to choose from, depending on your facility’s operation and workflow. Some of the common types of conveyors include:
Monorail Conveyors
- Overview: Monorail conveyors consist of a single rail with attachments for hanging parts. They are used for transporting parts through different stages of the washing and drying process.
- How it Works: Parts are suspended from the conveyor and moved along the rail, often through a series of wash and rinse cycles.
- Applications: Ideal for parts that need to be hung vertically and can be consistently spaced, such as automotive components or metal fabrications.
Flat Belt Conveyors (Inline and U-Bend)
- Overview: Flat belt conveyors feature a continuous flat belt on which parts are placed. The belt can move in a straight line (inline) or in a U-shaped path (U-bend).
- How it Works: Parts rest on the belt and are moved through the washing system. The belt’s speed can be adjusted to control the washing time.
- Applications: Suited for a variety of parts, particularly those that can lay flat and are not prone to tangling or damage from contact with other parts.
Dual-Strand Chain Conveyors
- Overview: These conveyors use two parallel chains with fixtures to hold specific parts in place.
- How it Works: Parts are secured on the fixtures and conveyed through the washing system, ensuring precise positioning and orientation.
- Applications: Best for parts that require specific orientations or have irregular shapes that need to be secured, such as engine blocks or intricate metal parts.
Gravity Feed Roller/Conveyors
- Overview: Gravity feed roller conveyors use the force of gravity to move parts along rollers.
- How it Works: Positioned at a slight decline, parts move over rollers by gravity, often used as a feeding system into another conveyor type.
- Applications: Useful for lightweight parts or as a cost-effective solution for moving parts from a higher elevation to a lower one.
Power-Roller Conveyors
- Overview: Power-roller conveyors use powered rollers to move parts.
- How it Works: Each roller is motorized, providing consistent and controlled movement of parts.
- Applications: Ideal for heavier parts or when precise control over the speed and movement of parts is necessary.
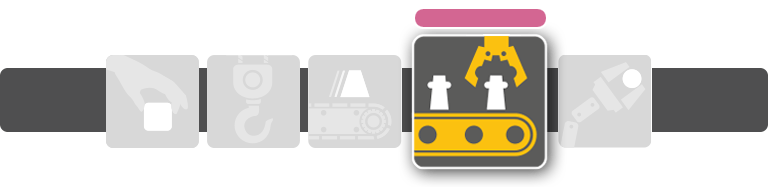
Pick and Place Systems
Pick and place systems are a step towards advanced automation and are considered semi-automated systems. They use mechanical arms or pneumatic systems (like a robot) to grip and place the parts from conveyors into the industrial parts washing machine. This semi-automated approach is more precise and consistent than manual handling.
This pneumatic-type machine is not as flexible as a robot and may require redesigning if changes are made to the machine or process flow. It reduces labor needs and eliminates ergonomic concerns while transferring parts efficiently.
Pick and Place Considerations
- Reduced Labor Dependency: Lower labor costs and less ergonomic risk.
- Moderate Flexibility: Can be reconfigured for different parts but may require additional investment.
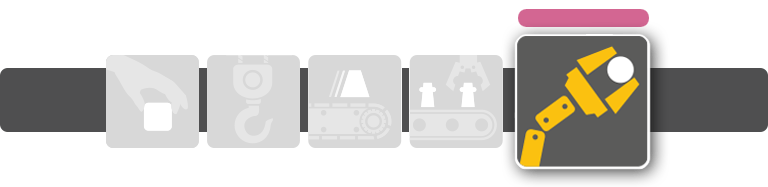
Fully Automated Systems (Robot Integrated)
Fully automated systems are the pinnacle of automation in industrial part washing systems. These systems use robotic arms for handling parts, allowing for hands-free parts handling. These systems are often integrated with conveyors to further streamline the washing process.
Fully automated systems offer the highest efficiency and precision. They can eliminate the need for operators and are ideal for high production rates as they can operate continuously (24/7) without taking breaks.
They are ideal for high-volume, high-variability production environments.
Fully Automated Considerations
- Maximized Efficiency: Ideal for continuous, high-volume operations.
- Adaptability: Robots are flexible and easily reprogrammable for different parts and processes.
- Long-Term Cost Benefits: Higher initial investment but significant long-term savings in labor and efficiency.
Conclusion
The spectrum of automation in industrial parts washing systems encompasses a diverse array of solutions, each tailored to meet varying operational demands. From the simplicity of manual systems to the sophistication of advanced robotic automation, comprehending these options is key to making informed decisions for optimizing manufacturing processes.
A clear understanding of this spectrum aids in aligning automation choices with operational needs and workforce capabilities, thereby enhancing overall efficiency.
Here’s a high-level overview of the various automation levels:
- Complete Manual Systems: Fundamental and labor-intensive, ideal for small-scale operations where manual handling is feasible.
- Hoist-Loaded Systems: A blend of manual effort and mechanical assistance, employing hoists or cranes to ease the physical strain on operators in a semi-automated environment.
- Conveyorized Systems: A significant advancement in automation, utilizing conveyors to facilitate parts movement, accommodating a wide range of parts and processes.
- Pick and Place Systems: A move towards more sophisticated automation, employing pneumatics or mechanical arms for precise placement of parts, reducing labor costs and ergonomic risks.
- Fully Automated Systems (Robot Integrated): The epitome of automation technology, featuring robotic arms for efficient parts handling, highly adaptable for high-volume, diverse operations.
Each automation level offers unique benefits and considerations, significantly boosting efficiency and fitting specific production needs. By carefully aligning your system choice with these operational requirements, you can ensure efficient, streamlined operations, and prepare your workforce for the future, staying ahead of evolving manufacturing trends.
Ready to Elevate Your Industrial Washing Processes?
Discover the ideal automation solution for your industrial parts washing needs with ALMCO. Our expertise in a wide range of washing and drying systems ensures that you receive tailored solutions that align perfectly with your operational requirements.
Don’t let the complexities of automation overwhelm you. Our team is here to guide you through every step, from understanding the basics to implementing the most advanced systems.
Reach out to us today to explore how we can enhance your production efficiency with the perfect automation level:
- Call Us: 1-800-521-2740 | 507-377-2102
- Email Us: sales@almco.com
Let ALMCO be your partner in driving innovation and efficiency in your industrial processes. We’re more than just a provider; we’re your partner in progress.