ROTARY DRUM PARTS WASHERS
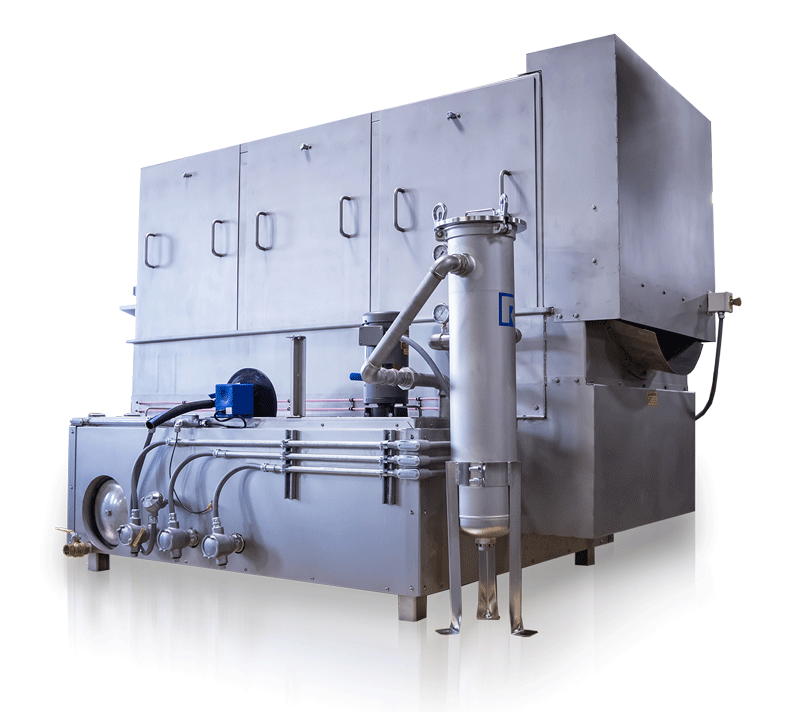
Ideal for Mass Production Applications
Rotary Drum Washers are ideal for washing parts in a mass production application. Some applications of Rotatory Drum Washers include stamped parts, fasteners, and ammunition. Parts can be washed in batches, or used in a complete through-feed operation. Hence, this allows you to feed the parts directly from the washer section to a rotary drying system, if required.
The length of the drum can be fully customized based on the customer’s preference. The required helix spacing, and diameter of the machine, in turn, is determined by the parts being washed.
There are many drum material options making the Rotary Drum Washer ideal for small parts that would be difficult to wash in a belt, cabinet, or agitation washer.
Parts are spiraled through the cleaning drum chamber via the helix auger and are submerged in liquid and sprayed via a nozzle-equipped manifold for complete tumbled cleaning. Parts may pass through various soak, wash, drain, and rinse sections. Rust inhibitor and drying sections are also available.
Rotary Drum Washers vary in auger pitch and drum diameter based on the following specifications:
- Standard inner drum diameters are 18’’, 24’’, 30’’, and 36’’.
- The standard helix auger inside the drum has a 12’’ pitch, with optional 3’’ increments. The smallest available pitch is 6’’.
Features
- Multiple process stages configured for your application
- Stainless steel construction
- Variable speed drum with sizes from 18″ to 36″ diameter
- Processing drum with continuous weld on both sides of helix
- Removable stainless steel chip tray in wash
- Heated tanks
- Float switch for heater protection
- Automatic water and compound replenishment
Options
- Bag filtration system (mild steel or stainless steel)
- Oil skimmer or coalescer
- Insulated wash and rinse tanks
- Vapor exhaust duct connections and vapor exhaust system
- PLC and touch screen controls
- Product lifters
- Stainless steel or mild steel filter housings
- UL 508A electrical controls