If you are in the manufacturing industry, then you know how important it is to have clean parts. That’s where aqueous parts washers play an important role.
Aqueous parts washers use water-based cleaning solutions to remove dirt, grease, and grime from parts, offering effective solutions for industrial cleaning needs. These machines come in different types and sizes, each with unique features that make them suitable for specific applications.
When it comes to choosing an aqueous parts washer, there are so many options that you may feel overwhelmed. The decision-making process can be complex given the various factors you need to consider, such as the size and materials of your parts, the type of contaminants you must remove, your upstream and downstream workflow, and the level of throughput you need – just to name a few!
When working with an aqueous parts washer manufacturer or supplier, it’s crucial to ask the right questions to make sure the machine you’re investing in aligns perfectly with your needs.
So, before you make a decision, take a moment to ponder: What are the key factors that will determine which aqueous parts washer is right for you?
Table of Contents
- Part Characteristics: Shape, Dimensions, Weight & Material
- Upstream & Downstream Workflow Integration
- Production Volume, Rates & Goals
- Cleanliness & Dryness Specifications
- Overall Machine Footprint
- Energy Requirements & Compliance
- Automation Level
- Budget & ROI Expectations
Key Takeaways
- Understand how your parts’ characteristics, including shape, dimension, weight, and material greatly affects your choice of aqueous parts washer.
- Reflect on your upstream and downstream workflow to guide your washer selection.
- Consider production volume, cleanliness & dryness specifications, and machine footprint for optimal machine alignment.
1. Part Characteristics: Shape, Dimensions, Weight & Material

Selecting the right aqueous parts washer is a process that involves more than just assessing the machine’s capabilities; it requires a thorough understanding of the parts themselves.
This section explores the crucial role part shape, dimension, and material play in selecting an aqueous parts washer and are arguably the most important to your equipment considerations.
Consider the following questions:
- Do your parts have intricate details, crevices, or blind holes?
- Do your parts have pockets or internal passages?
- Are your parts machined, inverted, or concave?
The Significance of Part Shape
The shape of a part significantly influences the type of parts washer required.
Complex shapes with intricate details, crevices, holes, or blind spots demand specific features in a washer to ensure thorough cleaning.
The washer’s ability to access and clean all parts of a component is crucial, especially for parts with unique or challenging geometries.
For example: A part with multiple blind spots might require a washer with advanced jet sprays to ensure every area is reached and cleaned.
Understanding the Impact of Part Dimensions and Weight
Part dimensions and weight are equally critical. Some washers are designed for smaller, lighter parts, while others cater to larger or heavier components. The size and weight of your parts will not only influence the type of washer needed but also the handling and loading mechanisms that are required, such as baskets or conveyors.
Example 1: Light parts might be challenging to wash or dry as they can be displaced by water sprays or by drying mechanisms.
Example 2: Heavy parts may require additional supports on various machine components. They may also require a hoist or crane to get them loaded and unloaded into the machine.
Dive further into: The Crucial Role Part Geometry, Size, and Weight Play in Selecting a Parts Washing Machine
Part Material Matters
Beyond your part’s shape and dimension, the material(s) of your parts or components is critical in considering what aqueous parts washer will be the best fit. Different materials demand different cleaning approaches.
Understanding your part(s) helps in selecting a washer that offers the appropriate cleaning and drying techniques and helps avoid part damage. Factors you should consider regarding part material include:
- Chemical compatibility: Your parts and machine may be incompatible with the wash solution, or the residue on the part may be resistant to certain chemical compounds.
- Temperature compatibility: Your parts may require a certain temperature for efficient cleaning or may be incompatible with high temperatures.
- Material hardness, density & porosity: Your parts may not be compatible with certain machines, likewise, factors like part porosity can affect your parts’ drying process.
Understanding these intricacies ensures that your chosen washer aligns perfectly with the unique characteristics of your components.
Dive further into these factors in: Material Matters: A Guide to Aqueous Parts Washer Selection
2. Upstream & Downstream Workflow Integration
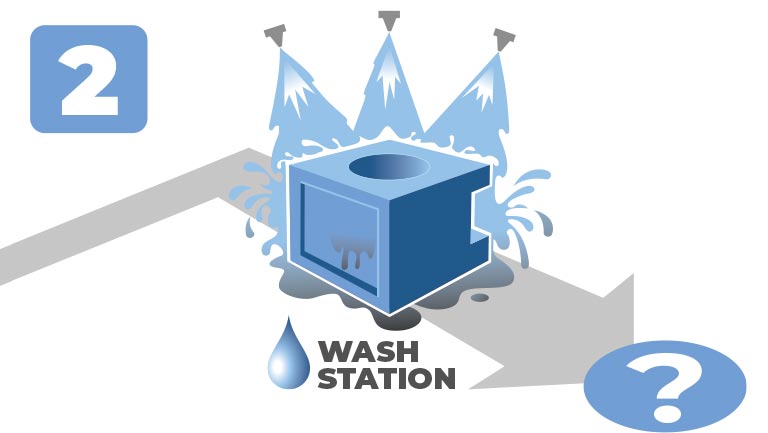
Reflecting on your past production processes and anticipating future requirements provides a roadmap for selecting an aqueous parts washer that seamlessly integrates into your workflow.
Upstream: What Step Are Your Parts Coming From?
Consider the residue on your parts as well as their soil level once leaving their previous production process (Tip: Soil level describes the amount of foreign material on a part, or how “dirty” a part is).
Consider the following questions:
- What is the upstream process before washing (what are we trying to clean off)?
- Is the residue a solid, liquid, or both?
- What is the soil level?
- How are the parts getting from the upstream process to the washer? (i.e. robot, conveyor, hand-loaded)?
Here are a few common upstream processes and the type of residue they typically leave behind:
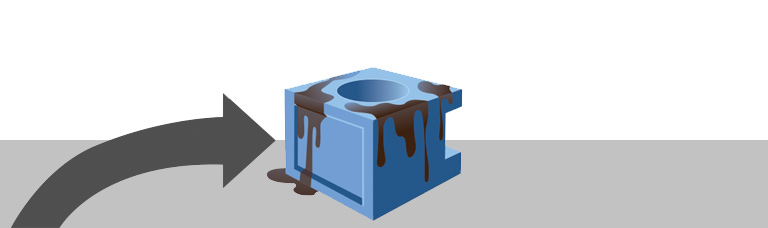
Upstream Process | Typical Residue |
Machining | Coolant & Chips |
Stamping/Forming | Oil |
Sand Casting | Oil & Sand |
Saw/Cutting | Coolant & Fines |
Grinding | Swarf |
Plasma Cutting | Soot |
Vibratory Deburring | Chemistry & Media Residue |
Rework/Remanufacturing | Oil, Grease, Dirt & Sand |
Rust Prevention (RP) Coating | RP Compound/Coating |
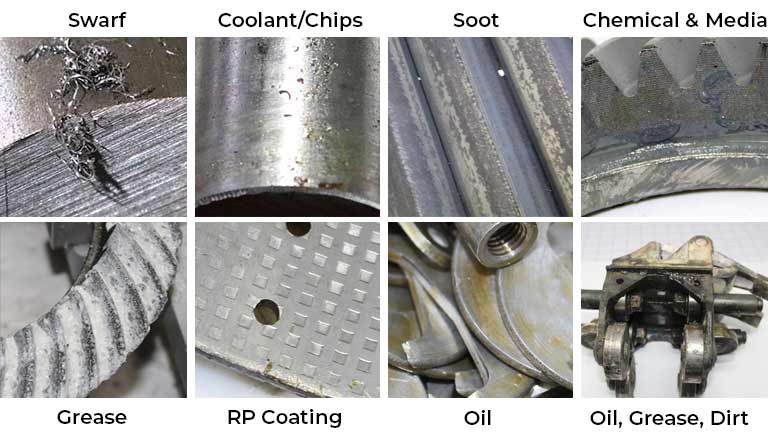
By understanding the residue on your parts and their soil level, you or your sales representative will have a better idea of what type of stages are needed for your aqueous washing system and the approximate duration needed at each stage for optimal results.
Dive further into the various aqueous parts washer stages in: Understanding the Essential Stages of Industrial Parts Cleaning
Downstream: What’s the Next Step in The Process?
Anticipate future processes and your final desired results – will your parts be moving into packaging, assembly, or another process?
Each of these processes requires a different level of cleanliness or dryness. Anticipating these aspects ensures that your aqueous parts washer is not just a standalone machine but is tailored to seamlessly integrate into your workflow.
For example: Some parts may need to be fully cleaned, treated, and dried before they are ready for the next downstream process or for the end user. Parts may need to go through a multistage process such as wash, rinse, rust inhibit, moisture blow-off, or drying stages – which are only available with certain parts washing equipment.
Therefore, it’s important to know what your end requirements are, and the exact type of residue on your parts.
Here are a few common downstream processes and what type of washing and drying stages are typically required:
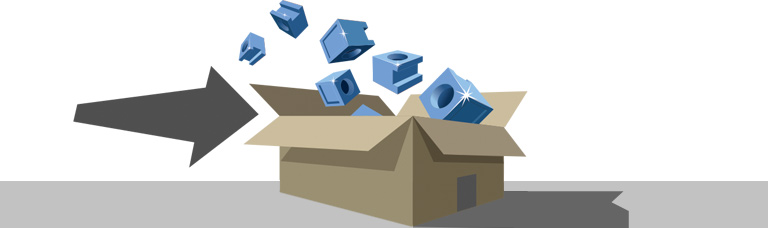
Downstream Process | Typical Stages Required |
Final Packaging (for customer) | Wash, Rinse, Blow-Off, Dry, Cool-Down |
Assembly/Handling | Wash, Rinse, Blow-Off, Dry, Cool-Down |
Plating | Wash, Rinse, Blow-Off, Dry |
Painting/Powder Coat | Wash, Rinse, Blow-Off, Dry |
Pressure Testing | Wash, Rinse, Blow-Off, Dry, Cool-Down |
Welding | Wash, RP Rinse, Blow-Off |
3. Production Volume, Rates & Goals
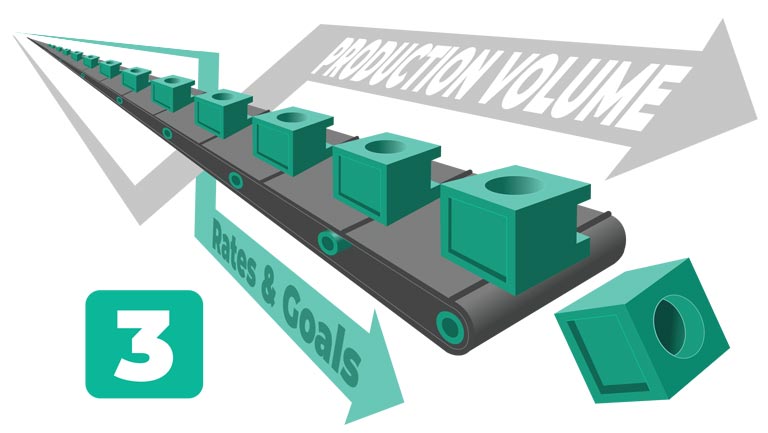
Understanding your production volume, desired rates, and overall goals is essential for selecting a machine that aligns with your operational scale. The volume and rate at which you produce parts impacts the type of machine needed.
For example: If you’re producing a few hundred parts versus tens of thousands annually your equipment requirements will differ significantly.
Consider your production rates and the frequency of operation. Are you running a continuous operation, or are you involved in short runs throughout the year?
Consider the following questions:
- What is your production rate?
- How many parts per hour/day do you need to reach?
- How many shifts do you operate per day/week?
- How many parts are you producing?
- What are the cycle times? Or what cycle times are you looking for?
The answers to these questions influence not only the size of the machine but also whether additional features are needed, such as conveyors to load and unload parts. By aligning your washer with your current and future production needs, you ensure that it complements the volume and flow of parts in your manufacturing process.
4. Cleanliness & Dryness Specifications
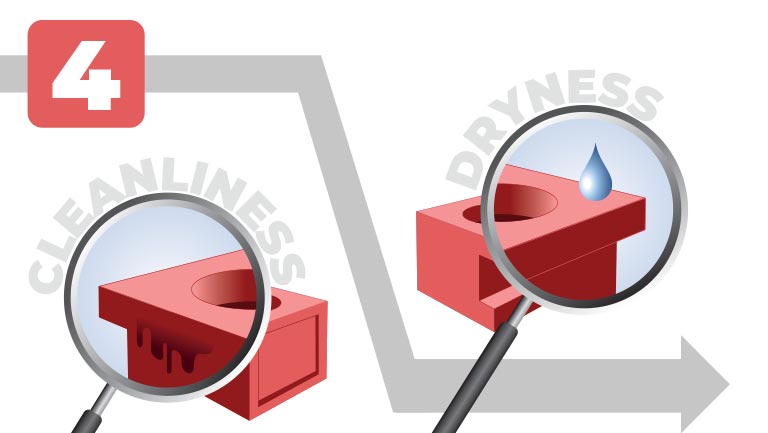
Different applications demand varying cleanliness and dryness levels. Many organizations have cleanliness or dryness specifications that need to be met due to their downstream processes.
It’s crucial to communicate any cleanliness specs or dryness requirements right away in your conversations to ensure your aqueous cleaning system meets your standards.
Cleanliness Specifications
Establishing cleanliness specifications involves defining the acceptable level of foreign material on a part. You may have cleanliness specs directly from your organization that need to be met.
When it comes to aqueous parts washing, cleanliness is not a one-size-fits-all concept. Some projects might achieve optimal cleanliness with just a few targeted cleaning stages, while others require a more complex, multi-faceted approach to meet stringent cleanliness and dryness specifications.
Due to this variability, selecting the most appropriate and efficient washing system requires understanding the unique requirements of your washing application.
Gain a deeper insight into the critical aspects of part washing in:
- The Crucial Role Part Geometry, Size, and Weight Play in Selecting a Parts Washing Machine
- Understanding the Essential Stages of Industrial Parts Cleaning
Dryness Requirements
While cleanliness specifications are critical, equally important are the dryness requirements of your parts post-washing. The dryness requirements directly affect your parts’ compatibility with downstream processes. These requirements dictate the type of machine needed, the number and types of stages required, and determine what specific drying techniques need to be considered.
Drying Stage: Tailored for Part Characteristics
Achieving the right level of dryness depends on the nature of the parts themselves:
- Material and shape considerations: Different materials and shapes can pose unique drying challenges. For instance, porous materials or complex geometries might retain moisture, requiring advanced drying methods.
- Temperature sensitivity: Some parts may be temperature-sensitive, requiring careful balancing of drying speed and temperature to avoid damage.
The drying process must be customized to ensure that parts are not only clean but also in the right state for subsequent handling or processing.
Challenges in Effective Drying
Effective drying is crucial for several reasons:
- Safety in handling: Parts need to be sufficiently dry and cool for safe handling in downstream processes. This is particularly important if operators are handling parts directly after washing or drying.
- Dimensional stability: High heat from drying can cause materials to warp or change size depending on their material. This is particularly crucial if pressure testing or dimension checks are conducted post-washing. Ensuring parts are not excessively heated is vital to maintain their dimensional integrity.
- Preventing rust and contamination: For parts going into packaging, complete dryness is vital. Any residual moisture can lead to condensation and rust, compromising the integrity of the part.
5. Overall Machine Footprint
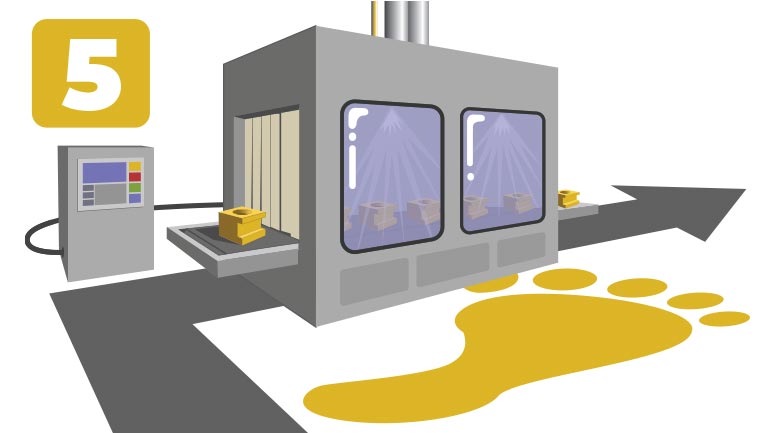
It is crucial to consider the overall footprint of the machine within the confines of your facility. Choosing a washer that fits seamlessly into your workspace is key. The layout, flow, and available floor space within your facility will influence what type of parts washing equipment is best suited for your operation.
For example: You may have limited space in your facility, work cells already in place, or may need to change the direction of workflow. You may even have large parts that require room for a hoist to efficiently lift parts.
Consider the layout of your facility and whether the machine needs to fit into an existing work cell. Industrial washing equipment can range from having a relatively small footprint, to very large. Depending on the number of stages needed for your washing process, additional space may also be required.
Consider the following questions:
- How much floor space do you have?
- Do you have a work cell already in place that it needs to fit into?
- Do you need to change the direction of the workflow?
- Do you have room for loading and unloading the parts (for a hoist, conveyors, etc.)?
- Have you accounted for utilities connections/hookups (i.e., water, gas, electric, steam)?
Assess the available floor space and evaluate if any adjustments are needed to accommodate the washer. Maintenance access is another critical consideration, ensuring that you can seamlessly access and maintain different components of the machine. By taking these factors into account, you ensure that your chosen aqueous parts washer fits seamlessly into your workspace.
6. Energy Requirements & Compliance
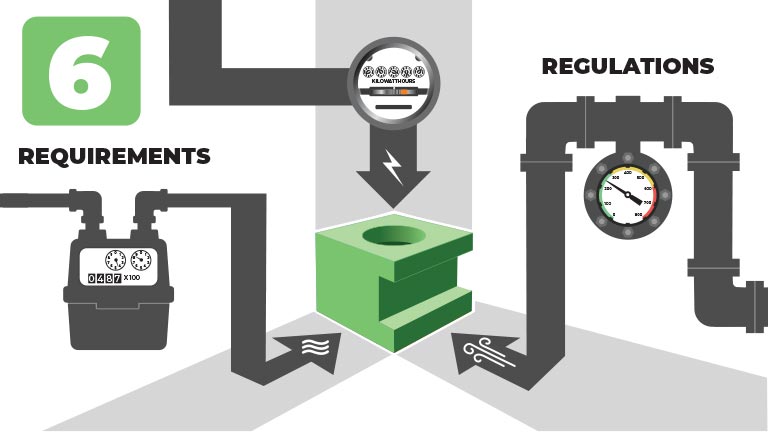
Considering the energy requirements and ensuring compliance with your facility, as well as your industry’s relevant regulations, is of key importance.
Energy Requirements
In understanding energy requirements, assess the pros and cons of each energy source and determine whether your preference is electric, gas, or steam heat. Align these preferences with your electrical capabilities, ensuring your electrical grid can support the aqueous parts washer and dryer system you need.
Example 1: There might already be a gas supply where you want to put your industrial cleaning system. You might be able to save money by utilizing your existing system instead of upgrading to electrical or steam energy.
Example 2: Gas energy typically has a higher upfront cost, but the utilities are often more cost-effective over time.
Energy Regulations and Compliance
In regards to ensuring compliance, both local, state, and environmental regulations will play a significant role in determining the suitability of the washer for your facility. We recommend speaking to your local utility provider to make sure you’re in compliance with any applicable codes for your area.
By addressing questions related to electrical requirements and regulatory compliance, you not only enhance the efficiency of your operations but also contribute to environmentally responsible manufacturing practices.
For example: Will the addition of natural gas exhaust from the equipment require a change in your facility’s air permit?
Dive Deeper: Understanding Energy Sources for Industrial Parts Washing Machines: Pros, Cons, & FAQs
7. Automation Level
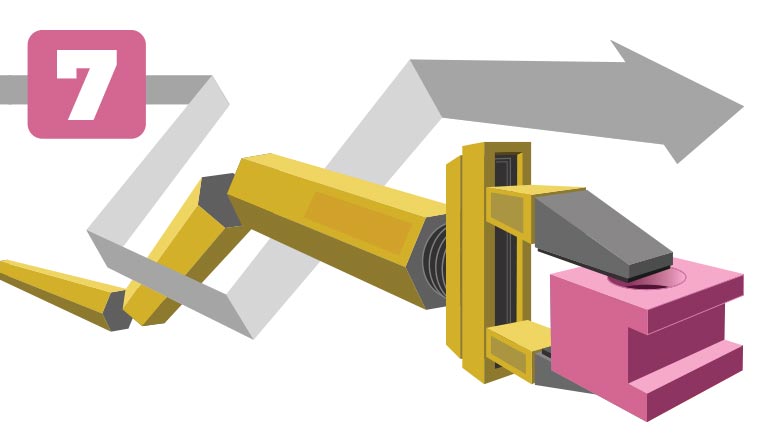
Exploring the automation capabilities of your industrial parts washer can significantly enhance efficiency, aligning with modern manufacturing trends. From simple pick-and-place loading to complex, unmanned operations, automation opens avenues for streamlined processes. It’s not just about the capability of the machine but also how well it integrates with your workforce.
Consider the level of automation needed for your operations. Are you looking for a fully automated system, or do you prefer a more manual approach? It is also important to assess the number of people dedicated to your parts loading and unloading process.
For example: A large washer may require multiple personnel for efficient operation.
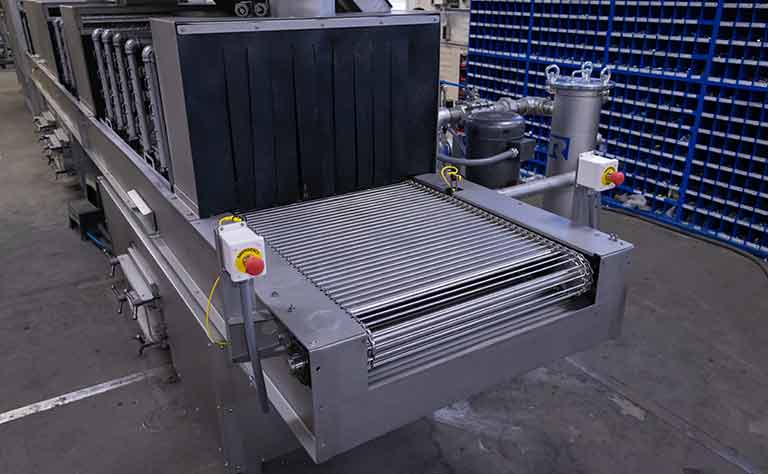
By understanding your automation needs, you not only streamline processes but also optimize the utilization of your workforce.
Dive deeper into the spectrum of industrial parts washer automation: The Spectrum of Automation in Industrial Parts Washing Systems
8. Budget & ROI Expectations
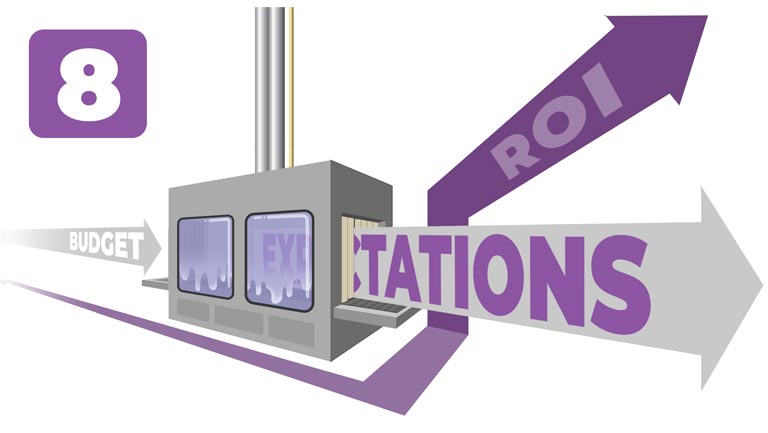
Evaluate your budget constraints and set realistic ROI expectations. Striking a careful balance between cost and expected returns is vital for a successful investment. When considering your budget, don’t just focus on the upfront costs; consider the long-term value that the equipment brings to your operations.
Understanding the Differences
Understand the differences in construction, components, and material used in various types of aqueous parts washers.
For example: Equipment constructed of high-grade stainless steel may have a higher upfront cost, but it can offer significantly more years of use and a higher ROI compared to equipment made with lower-grade materials.
Cost Beyond the Purchase
Consider not just the cost of the machine, but its cost of operation, including cycle times, throughput, and downtime. This broader perspective is key to achieving a higher ROI over the machine’s lifespan.
Calculating ROI for Industrial Parts Washing Equipment
It is important to conduct an ROI analysis to understand both the costs and benefits of investing in industrial parts washing equipment. Equipment manufacturers can often assist with creating an accurate ROI calculation to assist in the decision-making process and show the acquisition’s financial viability.
When creating a return on investment (ROI) calculation for industrial parts washing equipment, consider these factors:
- Evaluate the initial investment costs, including the purchase price of the equipment, installation expenses, and any additional infrastructure requirements.
- Assess the operational costs, like energy consumption, water usage, maintenance, and consumables like cleaning agents and filters. Determine the expected lifespan of the equipment and incorporate depreciation.
- Quantify the anticipated labor savings and increased productivity resulting from the efficiency of the new equipment.
- Account for any potential reductions in rework or rejects due to improved cleaning quality. Consider regulatory compliance and environmental benefits that may contribute to cost savings or goodwill.
- Factor in the potential resale value of the equipment at the end of its useful life.
Together, all these factors will give you a clear picture of the impact of your investment. By weighing the immediate costs against long-term benefits and operational improvements, this ROI analysis will help ensure that buying industrial parts washing equipment is a smart, financial move for your organization.
Financing Considerations
To make capital equipment purchases more manageable, ALMCO offers attractive financing options. These include fast credit decisions, deferred payment options, and no down payment requirements. We invite you to explore these options on our financing page to calculate payments, discover potential tax benefits, and find a plan that suits your needs.
Conclusion
As you explore the multifaceted realm of aqueous parts washers, these 8 key factors are your compass for a well-informed decision.
- Part Characteristics: Shape, dimension, and material greatly influence washer choice.
- Workflow Integration: Assess both upstream and downstream workflows for alignment.
- Production Volume: Align with your operational scale, considering volume and rate.
- Cleanliness & Dryness Specs: Ensure the washer meets your specific cleanliness and dryness needs.
- Space Efficiency: Consider the machine’s footprint in relation to your facility’s layout.
- Energy & Compliance: Factor in energy requirements and regulatory compliance.
- Automation Level: Decide on the degree of automation required for efficiency.
- Budget & ROI: Evaluate costs, long-term value, and potential returns.
Whether you’re in conversation with a sales representative or conducting independent research, an understanding of these considerations will empower you to make an informed decision.
Frequently Asked Questions
What is an aqueous parts washer?
Aqueous parts washers are industrial washing machines that use water-based cleaning solutions to remove dirt, grease, and grime from parts. These washers are commonly used in the manufacturing industry. Unlike household washers, they tackle industrial grime, offering effective solutions for the manufacturing sector’s cleaning needs.
How does an aqueous parts washer work?
Aqueous parts washers utilize water-based cleaning solutions in a five-stage process: washing, rinsing, moisture blow-off, drying, and cool-down. During washing, parts are sprayed or submerged in a cleaning solution, removing contaminants. Rinsing often follows, eliminating any residual solution. In moisture blow-off and drying stages, blow-off nozzles, hot air, or vacuum drying is used to dry the parts. Cool-down is typically the last stage and utilizes an extended length of dryer or conveyor belt to continue to dry or cool the parts.
What is aqueous washing?
Aqueous washing involves using water-based solutions to clean parts and remove contaminants such as dirt and grease. This environmentally friendly method provides an effective and safe alternative to traditional solvent-based cleaning processes.
What are the types of aqueous parts washers?
There are various types of aqueous parts washers available in the market, including conveyor washers, cabinet washers, immersion washers, rotary drum washers, and ultrasonic washers. Each type of washer has its own unique features and benefits, and the one you choose will depend on your specific needs.
What are the differences between a heated and non-heated aqueous parts washer?
A heated aqueous parts washer uses a heating element to warm the cleaning solution to a higher temperature, which enhances the cleaning process. A non-heated parts washer does not have a heating element and relies on ambient temperature to clean the parts. Heated parts washers are more effective at removing stubborn dirt and grime, but they are more expensive to operate because of the energy required to heat the solution.
What is the difference between aqueous and solvent?
The key difference between aqueous and solvent washers lies in the cleaning agents. Aqueous solutions use water-based cleaning agents, which are more environmentally friendly and safer. In contrast, solvent-based methods use chemical solvents, which can be harsh and potentially harmful. Aqueous cleaning is often a more sustainable and safer alternative to solvent-based processes.