In the quest for the ideal aqueous parts washer, understanding the interaction between part material and washer specifications is crucial. By thoroughly understanding the material characteristics of your parts, you can select an aqueous parts washer that not only cleans efficiently but also preserves the integrity and functionality of your parts.
This article highlights key considerations regarding the materials of your parts, with relevant examples, to aid in your decision-making process.
Consider the following questions:
- Is there any concern of part-on-part contact?
- What materials are your parts made of? Are there any temperature limits?
- What are the downstream processes?
Chemical Compatibility
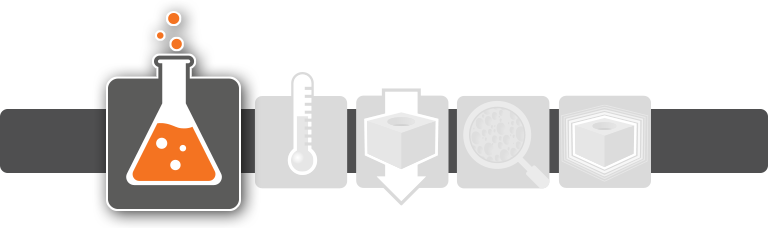
Your parts and machine may be incompatible or resistant to certain chemical compounds.
It’s essential to match the chemical properties of the cleaner with the material of the part to prevent damage. Some chemicals may be good at cleaning but could dissolve or remove the part material.
Example: Using the wrong cleaner can discolor aluminum or dissolve brass. For instance, mild steel cleaners might turn brass parts a different color.
Likewise, depending on the chemical needed to clean your part effectively, you may need to design your parts washing machine or machine components from a specific material to prevent damage to your cleaning system.
Example 1: You may need to use low-carbon stainless steel in the design of your parts cleaning machine to prevent erosion (this is especially true for certain chemistry used in cleaning such as cleaners with high alkalinity or high pH levels).
Example 2: A plastic tank may need to be utilized in machines such as an Immersion Washer or machine with a dip tank depending on the chemical compounds used in your application.
Having explored the crucial aspect of chemical compatibility, let’s now delve into how temperature plays a pivotal role in selecting the right aqueous parts washer.
Temperature Compatibility
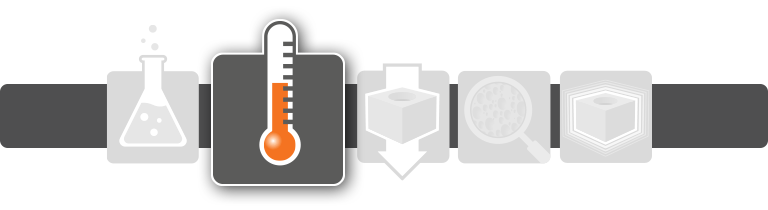
Temperature plays a crucial role in the cleaning process. Your parts may require a certain temperature for efficient cleaning or may be incompatible with high temperatures.
Example 1: For temperature-sensitive materials like plastics, too high of heat can warp, melt, or damage the parts.
Heat restrictions can also cause issues, as they can impact the effectiveness of the cleaning solution and the drying stage.
Example 1: Some chemicals may foam badly if they are not heated to a certain temperature.
Example 2: Some chemical solutions have temperature minimums and maximums – this can negatively affect the cleaning process if your part requires or can’t exceed a specific temperature.
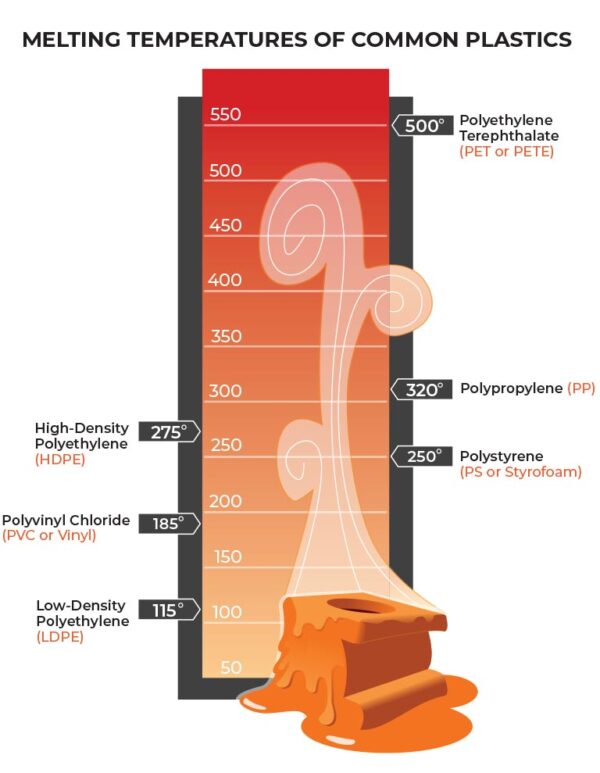
With a better understanding of temperature considerations, the next step is to examine the implications these factors have on downstream processes.
Downstream Process Implications
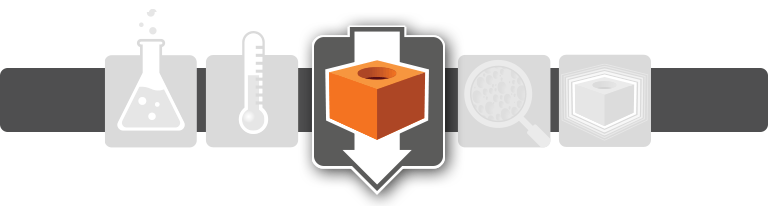
The choice of parts washer and cleaning agents must align with downstream processes like painting, plating, or assembly. It’s essential to select a system that won’t adversely affect these processes.
Since materials can warp or change size under high heat, pressure testing, and dimension checks could be significantly impacted if performed after high heat is used.
The following are some examples of downstream processes and the typical washing or drying stages required:
Downstream Process | Typical Stages Required |
Final Packaging (for customer) | Wash, Rinse, Blow-Off, Dry, Cool-Down |
Assembly/Handling | Wash, Rinse, Blow-Off, Dry, Cool-Down |
Plating | Wash, Rinse, Blow-Off, Dry |
Painting/Powder Coat | Wash, Rinse, Blow-Off, Dry |
Pressure Testing | Wash, Rinse, Blow-Off, Dry, Cool-Down |
Welding | Wash, RP Rinse, Blow-Off |
Now that we have discussed the impact on downstream processes, it’s important to consider how material properties like hardness, density, and porosity affect washing efficacy.
Material Hardness, Density & Porosity
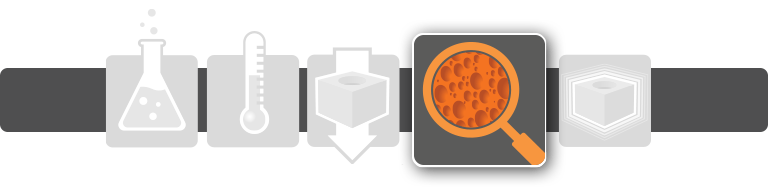
The hardness, density, and porosity of a part also dictate its suitability for certain washers.
Material Hardness
Softer or cosmetic parts, such as those made from yellow metals or aluminum, risk damage in certain washers due to scratching or part-on-part contact.
Example: Due to the soft nature of these materials, Drum Washers are not typically very compatible because the parts may scratch each other as they tumble and create part-on-part damage. Likewise, brittle materials may not be a good fit as they may break.
Conversely, harder materials can endure more vigorous cleaning processes, and will typically be compatible with more cleaning systems.
Material Density
The density and surface area-to-weight ratio influence how parts interact within the washer.
Lightweight parts with small or large surface areas could be displaced or damaged during washing, while heavy parts could require more washer modifications for additional support and handling.
Example 1: Lightweight parts such as small stampings often get blown around from the water pressure or air used during the washing or blow-off stages. This can cause part damage.
Example 2: Heavy parts may require additional belt rollers on the belt if a Belt Washer (such as Inline and U-Bend) is being used for the cleaning application.
Example 3: Cabinet Washers may need additional turntable supports if the parts are too heavy.
Example 4: Heavy parts may require specialized systems such as a hoist or crane for loading and unloading into the washer.
Material Porosity
Porosity varies significantly across materials, affecting drying processes. Managing these variations is critical in preventing damage and ensuring cleanliness.
Example 1: Powdered metal parts, despite appearing dry, can retain water and be prone to rusting due to their porosity.
Example 2: Printed parts may absorb solutions and their wash time may need to be limited.
Conclusion
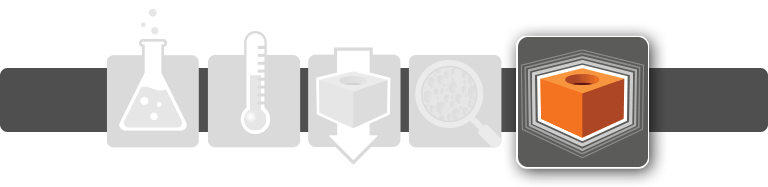
Selecting the right aqueous parts washer requires a nuanced understanding of part material characteristics. From chemical interactions to temperature limits and porosity, each factor plays a pivotal role in determining the most suitable equipment for your needs.
Selecting the right aqueous parts washer requires careful consideration of a variety of part characteristics including:
- Chemical compatibility
- Temperature compatibility
- Material hardness, density, and porosity
Remember, the right washer not only ensures effective cleaning but also prevents damage to parts. We recommend consulting with experts and referring to chemical compatibility charts to make an informed decision.
For those seeking further guidance or looking to explore our range of solutions, we invite you to contact one of our product experts at ALMCO. You can reach us by phone at 1-800-521-2740 or 507-377-2102, or via email at sales@almco.com. Our team is ready to provide tailored advice and support to meet your specific needs.