Navigating the world of parts washing can be a daunting task. It’s easy to feel overwhelmed amidst the sea of options available.
In this article, we’re going to discuss how the intricacies of your parts or components greatly impact your choice of parts washing machine. We could even argue that these factors are the most crucial to consider when researching the right equipment for your application.
These intricacies include:
- Part geometry
- Part size
- Part weight
- Part material (covered separately)
We’ll also share real-life examples from a variety of industries on how these factors played a significant role in the choice of our customers’ industrial parts washing system.
So, let’s dive in!
There’s No Universal Rulebook
You may be looking for the Holy Grail or an Ultimate Guide that will tell you exactly what piece of equipment will work for your specific part. Here’s the catch – there’s no universal guide to decide which equipment will serve your specific needs.
Every part and every cleaning application is unique, there’s no one-size-fits-all cleaning solution. We could talk for hours, days, (even years!) about how part geometry or the excess/absence of weight influenced a customers’ decision to choose or rule out a particular style of parts washer.
When making decisions about your application, there’s no substitute for consulting with a knowledgeable product specialist who can guide you through this decision-making process.
That’s why we highly recommend consulting with a specialist before deciding on a specific type of industrial parts washer. Having this conversation is key to choosing a machine that meets your exact requirements.
Sample Parts Processing
A great place to start in your search for the ideal parts washing machine is sending your parts in for sample part processing. Some companies offer this service for free to prove their finishing or washing machines and process will achieve your desired results.
Learn more about ALMCO’s free sample parts processing service
Part Geometry
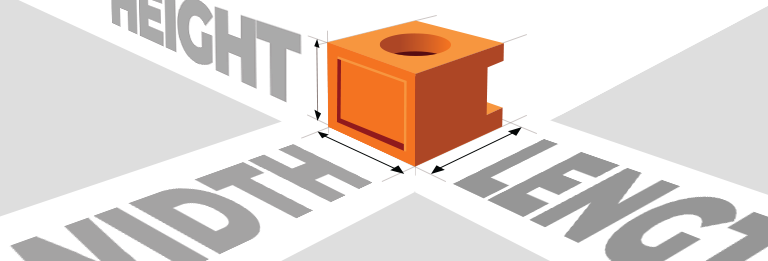
Delving into part geometry, we uncover the intricate details that define the effectiveness of a washing system. From the smallest crevice to the most complex surface, every geometric feature dictates the type of cleaning and machine required. Helping your product specialist understand these features is the first step in ensuring you find a parts washing machine perfectly suited to your parts.
When it comes time to get serious about parts washing systems, the challenge comes from the endless variety and complexity of part designs, each adding their own dimension to the discussion.
Questions to consider about your part(s):
- Are there intricate details, crevices, or blind holes?
- Are there pockets in your part, or internal passages?
- Are your parts machined, inverted, or concave?
If you answered “Yes” to any of these questions, it’s important to discuss these part features with a product specialist. Depending on the features of your part(s) you may need some form of customized cleaning solution.
For Example: Cleaning blind holes within a part is often difficult due to their geometry. The term “blind hole” is used to describe a hole that doesn’t go all the way through a part or component. Liquid or solid residue often gets stuck in these holes, making it difficult to effectively clean the parts.
Depending on the residue left in the blind hole, there are a few common methods that may work:
- Option 1: Utilize an aqueous parts washer that features custom spray nozzles. Line up a solid stream nozzle to spray directly at the hole to blast out the residue (chips, grease, etc.).
- Option 2: If a spray nozzle won’t work, use an ultrasonic immersion washer to fully submerge the part and break up the material within the blind hole that can’t be reached by a spray nozzle.
Note: These are 2 common solutions. However, there may be numerous other options depending on your part(s) and your cleanliness and dryness requirements.
While understanding the complexities of part geometry is crucial, it’s equally important to consider the size of the parts.
Part Size
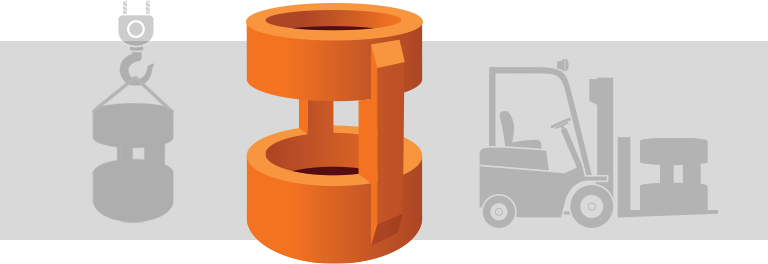
In addition to geometry, your parts’ dimensions play an important role in the cleaning process. Part size not only dictates the compatibility with washing systems but also influences the method and thoroughness of the cleaning process.
Some parts may be too small or too large for certain washing applications, and others might require special fixturing or baskets to prevent part damage or to contain them effectively. In any case, whether dealing with small or large parts, each size category brings its own set of challenges.
Questions to consider about your part(s):
- What size are the parts that you want to have processed?
- Are they too large or too small for standard parts washing machines?
- How will the part size impact the washing method?
- What is the scope? Are you processing 1 part or multiple types of parts at once?
- What is the surface area of your part(s)?
- What is the weight and length of the part(s) you need to process?
Small-Medium Sized Parts
There are a few common challenges that arise when washing small-medium sized parts.
They blow around: Small-medium sized parts often get blown around from the water or air pressure used during the washing or blow-off stages (if the washer is equipped with air or spray nozzles). This can cause part damage.
For example: Small stampings may not be suitable for a washer that utilizes high-pressure spray nozzles. Instead, they are often better-suited in either an immersion washer, where the parts can be fully submerged in a basket, or in a drum washer, where the parts are constantly tumbled within a helix-shaped barrel.
They get stuck: If not planned for properly, small-medium sized parts can be prone to getting stuck in machines.
For example: Most small part washing applications wouldn’t utilize a conveyor washing machine because they can fall through the belts on the conveyors. If a conveyor-style washer was used, baskets would likely need to be utilized to keep the parts contained.
They’re difficult to thoroughly clean: Small-medium parts often require specialized handling due to their size. Baskets are commonly used to keep them contained, which can make it difficult to get a thorough cleaning on the entire part surface.
Small-medium parts can also be prone to sticking and hard to separate and wash because of the surface tension of the liquid or residue on the parts.
For example: The solution is often utilizing a basket in an immersion washer. Drum washers are also a good application for small parts.
Large Sized Parts
The dimensions of large parts play a significant role in determining the suitable washing equipment for them. Large parts, due to their size, present unique challenges in the washing process. This might involve customizing the washing equipment.
Some of these challenges include:
Size constraints: Large parts may not fit in standard washers.
For example: An oversized component might be too tall or wide for a conventional washer. Each wash stage or section needs to be large enough to accommodate the part. Therefore, the total length of each stage will be much larger, leading to a much larger machine footprint.
Water transfer issues: Large parts, especially long ones, can transfer water from one washing stage to the next. This can cause contamination within your cleaning system’s other stages.
For example: In a conveyor washer, long components might require extended stages and additional drainage areas to prevent water carryover between stages.
Difficulty in achieving even cleaning: Ensuring that every part of a large component is equally cleaned can be challenging.
For example: In a cabinet washer, rotating the part or using multiple nozzles might be necessary for even cleaning.
With the size of the parts taken into account, another key aspect to consider is their weight.
Part Weight
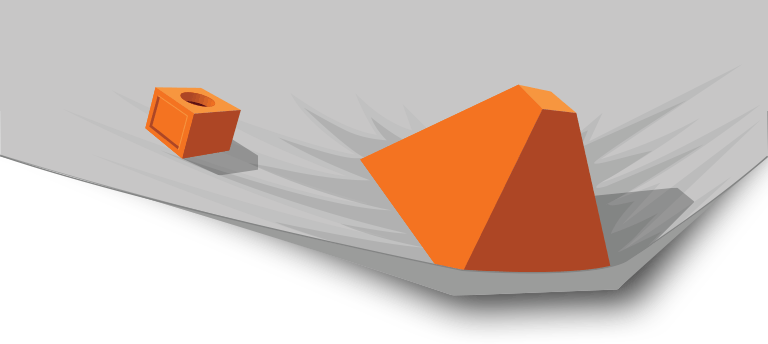
The heaviness or lightness of a part affects everything from the type of washing system you can use to the approach of handling and moving parts through the cleaning cycle. It’s a balancing act of matching part weight with the right washing technique.
Questions to consider about your part(s):
- How much do your parts weigh? Are they lightweight or heavy?
- What are your plans for loading and unloading these parts?
Lightweight Parts
Lightweight parts pose a unique challenge in parts washing due to their susceptibility to damage during the cleaning process. The key is to ensure that they are cleaned effectively without being subjected to excessive force.
Handling considerations: Require delicate handling to prevent damage.
Cleaning methods: High-pressure cleaning might be too harsh and gentler techniques are often necessary.
For example: You may need to adjust the spray or blow-off pressure to ensure parts are not displaced during washing. Or you may choose to utilize an immersion washer to completely submerge the parts instead of using nozzles.
Heavy Parts
Heavy parts demand a robust approach to washing, where the focus is on managing their substantial weight and size without compromising on the cleaning effectiveness.
Heavy and bulky parts demand robust washing systems capable of supporting their weight. These parts often require equipment with stronger structural support and more powerful handling mechanisms.
Structural requirements: Need robust systems that can support their weight.
For example: In conveyor belt washers like an Inline or U-Bend, the conveyors must be sized to handle the weight of multiple parts. In cabinet or immersion washers, the turntable may also need additional supports.
Handling mechanisms: Require equipment with stronger support and more powerful handling mechanisms.
Equipment Considerations for Different Part Weights
When considering the equipment necessary for cleaning parts of varying weights, it is essential to understand the specific requirements and risks associated with each weight category.
Lightweight Parts
When dealing with lightweight parts, the primary concern is the risk of damage due to high-pressure spray or blow-offs. One equipment solution to address this issue is utilizing an Immersion Washer.
These washers offer an effective cleaning solution without causing harm to delicate parts. They work by fully submerging the parts in a cleaning solution, thereby avoiding the damage that can be caused by high-pressure cleaning methods.
Heavy Parts
In contrast, heavy parts require a different approach due to their substantial weight and the need for easy loading and unloading. One effective equipment solution for cleaning heavy parts is the use of Conveyor Washers. These washers are designed to support significant weight. They can be equipped with additional supports and sized to handle multiple heavy parts simultaneously.
Another viable equipment solution for heavy parts is the utilization of Cabinet and Immersion Washers. These washers can be tailored to the needs of heavy parts by configuring turntables with additional supports.
Example: ALMCO has experience in creating cabinet washers that can effectively handle parts weighing as much as 5,000lbs.
To further facilitate the handling of these heavy parts, the implementation of hoists or cranes with these washers can be considered. This addition aids in the easier loading and unloading of the parts, making the overall process more efficient.
Conclusion
It’s clear that the characteristics of your parts greatly impact your choice of parts washing machine. Understanding part geometry, size, and weight will help you to make a more informed decision when looking at part washing solutions. Each aspect comes with its own set of challenges and considerations, so a thorough understanding, and often expert advice is needed.
By engaging in early discussions with a product specialist, you can ensure that your chosen machine is not just a fit, but the perfect match for your parts’ specific cleaning needs.
At ALMCO, we specialize in providing top-notch solutions in industrial finishing and washing. We’re more than happy to go over your parts with you and your desired results to find the best piece of equipment for your operation. Contact us today for further information or to discuss how our solutions can benefit your industrial manufacturing processes.